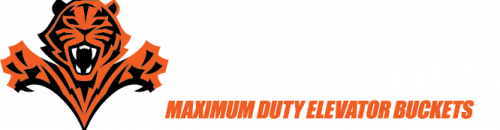
- The Original Maximum Duty Bucket!
- Rugged. Resilient. Reliable.
- Revolutionary Design that Changed an Industry!
- Heavy Front Lip for Digging
- Thicker Corners and Walls
- High Impact / Abrasion Resistant
- Decreases Elevator Down-Time
- Overview
- Size Chart
- Size Chart (Low Profile)
- Digger Bucket
- Uses
- Materials
- Venting
- Media / Literature
Tiger-Tuff is the original maximum duty elevator bucket. We designed and engineered it to increase bucket life. It lasts longer, so you replace fewer buckets, lowering downtime and maintenance costs. The Tiger-Tuff has proven its value over and over around the world. High volume applications are perfect for Tiger-Tuff. Minimum spacing is nominal projection plus 1”. The recommended belt width for a single row of buckets is actual bucket width plus 2″.
Tiger-Tuff Low Profile Option
A reduced back height for closer vertical spacing allows more buckets per foot of elevator belt. Open sides allow for optimal fill under less desirable elevator feeding conditions.
When upgrading to Low Profile buckets horsepower requirements must be evaluated due to increased capacity.
Other Considerations
DRILLING: Elevator buckets are manufactured without a drill pattern. Special drilling or punching can be accommodated upon customer request.
VENTING: Available as needed. See venting options in our catalog.
DIGGER BUCKETS: Use slightly larger metal digger elevator buckets to help loosen material in the elevator boot section that has set up or hardened, thereby reducing abrasion on the plastic buckets. Call for details on Metal Digger elevator bucket options.
SPACING: See elevator bucket spacing details in the size chart (depending on materials and speeds, smaller and larger spacing may be used).
INSTALLATION: Use a #1 standard elevator bolt or Sabre-Tooth elevator bolt for installation. Designed to be used with fender or flat and lock washers and hex or locking nuts. If buckets are being installed on chain, use hex head bolts, nuts and washers.
FDA: Both the urethane and polyethylene are designed to FDA specifications for direct contact with food products.
®5,343,839 The color orange, as it relates to buckets for agricultural and light industrial elevator type conveyors, is a United States registered trademark of Maxi-Lift Inc.
TMA986,627 The color orange, as it relates to buckets for agricultural and light industrial elevator type conveyors, is a Canadian registered trademark of Maxi-Lift Inc.
Tiger-Tuff Size Chart
Imperial/Metric conversion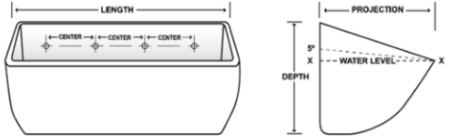
BUCKET SIZE | PUNCHING | WEIGHT, LBS. | CAPACITY, CU. IN. | ||||||||||||
---|---|---|---|---|---|---|---|---|---|---|---|---|---|---|---|
Bucket Size | Length | Projection | Depth | Back Wall Thickness | Centers | # of Holes | Bolt Size | Top Down | HDPE | Water Level | Usable 5 Deg. | Std Spacing | |||
in. | mm | in. | mm | in. | mm | ||||||||||
6 x 5 | 6-5/8 | 168 | 5-3/4 | 146 | 5 | 127 | 0.33 | 4-3/8 | 2 | 1/4 | 1-5/8 | 0.94 | 67.20 | 73.98 | 6 |
7 x 5 | 7-5/8 | 194 | 5-3/4 | 146 | 5 | 127 | 0.33 | 2-11/16 | 3 | 1/4 | 1-5/8 | 1.10 | 79.72 | 89.24 | 6 |
8 x 5 | 8-5/8 | 219 | 5-3/4 | 146 | 5 | 127 | 0.33 | 3-1/16 | 3 | 1/4 | 1-5/8 | 1.25 | 88.54 | 97.98 | 6 |
9 x 5 | 9-5/8 | 244 | 5-3/4 | 146 | 5 | 127 | 0.33 | 3-5/8 | 3 | 1/4 | 1-5/8 | 1.41 | 107.37 | 121.27 | 6 |
10 x 5 | 10-5/8 | 270 | 5-3/4 | 146 | 5 | 127 | 0.33 | 4-1/8 | 3 | 1/4 | 1-5/8 | 1.57 | 121.30 | 138.89 | 6 |
11 x 5 | 11-5/8 | 295 | 5-3/4 | 146 | 5 | 127 | 0.33 | 3 | 4 | 1/4 | 1-5/8 | 1.72 | 140.70 | 153.16 | 6 |
12 x 5 | 12-5/8 | 321 | 5-3/4 | 146 | 5 | 127 | 0.33 | 3-3/8 | 4 | 1/4 | 1-5/8 | 1.88 | 159.87 | 167.14 | 6 |
8 x 6 | 8-5/8 | 219 | 6-7/8 | 175 | 6 | 152 | 0.40 | 3-1/16 | 3 | 1/4 | 1-5/8 | 1.82 | 135.56 | 150.85 | 7 |
9 x 6 | 9-5/8 | 244 | 6-7/8 | 175 | 6 | 152 | 0.40 | 3-5/8 | 3 | 1/4 | 1-5/8 | 1.97 | 150.26 | 165.87 | 7 |
10 x 6 | 10-5/8 | 270 | 6-7/8 | 175 | 6 | 152 | 0.40 | 4-1/8 | 3 | 1/4 | 1-5/8 | 2.13 | 170.69 | 185.62 | 7 |
11 x 6 | 11-5/8 | 295 | 6-7/8 | 175 | 6 | 152 | 0.40 | 3 | 4 | 1/4 | 1-5/8 | 2.29 | 185.18 | 200.36 | 7 |
12 x 6 | 12-5/8 | 321 | 6-7/8 | 175 | 6 | 152 | 0.40 | 3-3/8 | 4 | 1/4 | 1-5/8 | 2.44 | 200.37 | 220.58 | 7 |
13 x 6 | 13-5/8 | 346 | 6-7/8 | 175 | 6 | 152 | 0.40 | 3-5/8 | 4 | 1/4 | 1-5/8 | 2.60 | 220.78 | 240.48 | 7 |
12 x 7 | 12-7/8 | 327 | 7-7/8 | 200 | 7 | 178 | 0.42 | 3-3/8 | 4 | 5/16 | 2 | 3.60 | 269.24 | 298.12 | 8 |
13 x 7 | 13-7/8 | 352 | 7-7/8 | 200 | 7 | 178 | 0.42 | 3-5/8 | 4 | 5/16 | 2 | 3.86 | 292.51 | 323.22 | 8 |
14 x 7 | 14-7/8 | 378 | 7-7/8 | 200 | 7 | 178 | 0.42 | 3 | 5 | 5/16 | 2 | 4.14 | 315.77 | 350.58 | 8 |
15 x 7 | 15-7/8 | 403 | 7-7/8 | 200 | 7 | 178 | 0.42 | 3-1/4 | 5 | 5/16 | 2 | 4.47 | 346.64 | 383.38 | 8 |
16 x 7 | 16-7/8 | 429 | 7-7/8 | 200 | 7 | 178 | 0.42 | 2-7/8 | 6 | 5/16 | 2 | 4.68 | 377.41 | 415.14 | 8 |
11 x 8 | 11-7/8 | 302 | 8-7/8 | 225 | 8-1/4 | 210 | 0.50 | 3 | 4 | 5/16 | 2 | 4.45 | 340.02 | 374.70 | 9 |
12 x 8 | 12-7/8 | 327 | 8-7/8 | 225 | 8-1/4 | 210 | 0.50 | 3-3/8 | 4 | 5/16 | 2 | 4.71 | 373.00 | 411.05 | 9 |
13 x 8 | 13-7/8 | 352 | 8-7/8 | 225 | 8-1/4 | 210 | 0.50 | 3-5/8 | 4 | 5/16 | 2 | 4.92 | 404.85 | 446.15 | 9 |
14 x 8 | 14-7/8 | 378 | 8-7/8 | 225 | 8-1/4 | 210 | 0.50 | 3 | 5 | 5/16 | 2 | 5.30 | 436.80 | 481.35 | 9 |
16 x 8 | 17 | 432 | 9-1/4 | 235 | 7-5/8 | 194 | 0.50 | 2-7/8 | 6 | 5/16 | 2-1/2 | 5.35 | 512.57 | 566.39 | 9 |
18 x 8 | 19 | 483 | 9-1/4 | 235 | 7-5/8 | 194 | 0.50 | 3-1/8 | 6 | 5/16 | 2-1/2 | 5.89 | 567.49 | 627.08 | 9 |
20 x 8 | 21 | 533 | 9-1/4 | 235 | 7-5/8 | 194 | 0.50 | 3-1/2 | 6 | 5/16 | 2-1/2 | 6.62 | 646.81 | 714.73 | 9 |
22 x 8 | 23 | 584 | 9-1/4 | 235 | 8-1/4 | 210 | 0.50 | 4 | 6 | 5/16 | 2-1/2 | 7.85 | 701.90 | 757.40 | 9 |
24 x 8 | 25 | 635 | 9-1/4 | 235 | 8-1/4 | 210 | 0.50 | 3-1/2 | 7 | 5/16 | 2-1/2 | 8.50 | 763.40 | 831.08 | 9 |
16 x 10 | 17 | 432 | 11-1/4 | 286 | 10 | 254 | 0.75 | 2-7/8 | 6 | 5/16 | 2-1/2 | 8.87 | 795.70 | 875.37 | 11 |
18 x 10 | 19 | 483 | 11-1/4 | 286 | 10 | 254 | 0.75 | 3-1/8 | 6 | 5/16 | 2-1/2 | 9.83 | 910.00 | 1001.21 | 11 |
20 x 10 | 21 | 533 | 11-1/4 | 286 | 10 | 254 | 0.75 | 3-1/2 | 6 | 5/16 | 2-1/2 | 10.57 | 1032.50 | 1135.98 | 11 |
Tiger-Tuff (Low Profile)
BUCKET SIZE | PUNCHING | WEIGHT, LBS. | CAPACITY, CU. IN. | ||||||||||||||
---|---|---|---|---|---|---|---|---|---|---|---|---|---|---|---|---|---|
Bucket Size | Length | Projection | Depth | Back Wall Thickness | Centers | # of Holes | Bolt Size | Top Down | HDPE | Nylon | Urethane | Water Level | Usable 5 Deg. | Std Spacing | |||
in. | mm | in. | mm | in. | mm | ||||||||||||
6 x 5 | 6-5/8 | 168 | 5-3/4 | 146 | 4 | 102 | 0.33 | 4-3/8 | 2 | 1/4 | 1 | 0.84 | – | – | 67.20 | 73.98 | 4 |
7 x 5 | 7-5/8 | 194 | 5-3/4 | 146 | 4 | 102 | 0.33 | 2-11/16 | 3 | 1/4 | 1 | 0.98 | – | – | 79.72 | 89.24 | 4 |
8 x 5 | 8-5/8 | 219 | 5-3/4 | 146 | 4 | 102 | 0.33 | 3-1/16 | 3 | 1/4 | 1 | 1.11 | – | – | 88.54 | 97.98 | 4 |
9 x 5 | 9-5/8 | 244 | 5-3/4 | 146 | 4 | 102 | 0.33 | 3-5/8 | 3 | 1/4 | 1 | 1.25 | – | – | 107.37 | 121.27 | 4 |
10 x 5 | 10-5/8 | 270 | 5-3/4 | 146 | 4 | 102 | 0.33 | 4-1/8 | 3 | 1/4 | 1 | 1.40 | – | – | 121.30 | 138.89 | 4 |
11 x 5 | 11-5/8 | 295 | 5-3/4 | 146 | 4 | 102 | 0.33 | 3 | 4 | 1/4 | 1 | 1.53 | – | – | 140.70 | 153.16 | 4 |
12 x 5 | 12-5/8 | 321 | 5-3/4 | 146 | 4 | 102 | 0.33 | 3-3/8 | 4 | 1/4 | 1 | 1.67 | – | – | 159.87 | 167.14 | 4 |
8 x 6 | 8-5/8 | 219 | 6-7/8 | 175 | 5 | 127 | 0.40 | 3-1/16 | 3 | 1/4 | 1 | 1.64 | – | – | 135.56 | 150.85 | 5 |
9 x 6 | 9-5/8 | 244 | 6-7/8 | 175 | 5 | 127 | 0.40 | 3-5/8 | 3 | 1/4 | 1 | 1.77 | – | – | 150.26 | 165.87 | 5 |
10 x 6 | 10-5/8 | 270 | 6-7/8 | 175 | 5 | 127 | 0.40 | 4-1/8 | 3 | 1/4 | 1 | 1.92 | – | – | 170.69 | 185.62 | 5 |
11 x 6 | 11-5/8 | 295 | 6-7/8 | 175 | 5 | 127 | 0.40 | 3 | 4 | 1/4 | 1 | 2.06 | – | – | 185.18 | 200.36 | 5 |
12 x 6 | 12-5/8 | 321 | 6-7/8 | 175 | 5 | 127 | 0.40 | 3-3/8 | 4 | 1/4 | 1 | 2.20 | – | – | 200.37 | 220.58 | 5 |
13 x 6 | 13-5/8 | 346 | 6-7/8 | 175 | 5 | 127 | 0.40 | 3-5/8 | 4 | 1/4 | 1 | 2.34 | – | – | 220.78 | 240.48 | 5 |
12 x 7 | 12-7/8 | 327 | 7-7/8 | 200 | 5-3/4 | 146 | 0.42 | 3-3/8 | 4 | 5/16 | 1 | 3.24 | 3.55 | 3.98 | 269.24 | 298.12 | 6 |
13 x 7 | 13-7/8 | 352 | 7-7/8 | 200 | 5-3/4 | 146 | 0.42 | 3-5/8 | 4 | 5/16 | 1 | 3.47 | 3.82 | 4.29 | 292.51 | 323.22 | 6 |
14 x 7 | 14-7/8 | 378 | 7-7/8 | 200 | 5-3/4 | 146 | 0.42 | 3 | 5 | 5/16 | 1 | 3.73 | 4.07 | 4.56 | 315.77 | 350.58 | 6 |
15 x 7 | 15-7/8 | 403 | 7-7/8 | 200 | 5-3/4 | 146 | 0.42 | 3-1/4 | 5 | 5/16 | 1 | 4.02 | 4.19 | 4.72 | 346.64 | 383.38 | 6 |
16 x 7 | 16-7/8 | 429 | 7-7/8 | 200 | 5-3/4 | 146 | 0.42 | 2-7/8 | 6 | 5/16 | 1 | 4.21 | 4.32 | 4.84 | 377.41 | 415.14 | 6 |
11 x 8 | 11-7/8 | 302 | 8-7/8 | 225 | 6-3/4 | 171 | 0.50 | 3 | 4 | 5/16 | 1 | 4.01 | 4.33 | 5.08 | 340.02 | 374.70 | 7 |
12 x 8 | 12-7/8 | 327 | 8-7/8 | 225 | 6-3/4 | 171 | 0.50 | 3-3/8 | 4 | 5/16 | 1 | 4.24 | 4.58 | 5.45 | 373.00 | 411.05 | 7 |
13 x 8 | 13-7/8 | 352 | 8-7/8 | 225 | 6-3/4 | 171 | 0.50 | 3-5/8 | 4 | 5/16 | 1 | 4.43 | 4.66 | 5.60 | 404.85 | 446.15 | 7 |
14 x 8 | 14-7/8 | 378 | 8-7/8 | 225 | 6-3/4 | 171 | 0.50 | 3 | 5 | 5/16 | 1 | 4.77 | 5.02 | 5.99 | 436.80 | 481.35 | 7 |
16 x 8 | 17 | 432 | 9-1/4 | 235 | 6-3/4 | 171 | 0.50 | 2-7/8 | 6 | 5/16 | 1 | 4.82 | 5.68 | 6.96 | 512.57 | 566.39 | 7 |
18 x 8 | 19 | 483 | 9-1/4 | 235 | 6-3/4 | 171 | 0.50 | 3-1/8 | 6 | 5/16 | 1 | 5.89 | 6.39 | – | 567.49 | 627.08 | 7 |
20 x 8 | 21 | 533 | 9-1/4 | 235 | 6-3/4 | 171 | 0.50 | 3-1/2 | 6 | 5/16 | 1 | 6.62 | 6.94 | – | 646.81 | 714.73 | 7 |
22 x 8 | 23 | 584 | 9-1/4 | 235 | 6-3/4 | 171 | 0.50 | 4 | 6 | 5/16 | 1 | 7.85 | 8.45 | – | 701.90 | 757.40 | 7 |
24 x 8 | 25 | 635 | 9-1/4 | 235 | 6-3/4 | 171 | 0.50 | 3-1/2 | 7 | 5/16 | 1 | 8.50 | 9.27 | – | 763.40 | 831.08 | 7 |
16 x 10 | 17 | 432 | 11-1/4 | 286 | 8-1/2 | 216 | 0.75 | 2-7/8 | 6 | 5/16 | 1 | 8.87 | 9.12 | – | 795.70 | 875.37 | 9 |
18 x 10 | 19 | 483 | 11-1/4 | 286 | 8-1/2 | 216 | 0.75 | 3-1/8 | 6 | 5/16 | 1 | 9.83 | 10.17 | – | 910.00 | 1001.21 | 9 |
20 x 10 | 21 | 533 | 11-1/4 | 286 | 8-1/2 | 216 | 0.75 | 3-1/2 | 6 | 5/16 | 1 | 10.27 | 11.02 | – | 1032.50 | 1135.98 | 9 |
Digger buckets are slightly larger to aid in breaking up material adhesions in a bucket elevator. Diggers extend 1/4″ further than plastic elevator buckets. Weights and dimensions will vary. Tolerance is a 1/4″ on all bucket dimensions except bolt hole diameter which is 1/16″. Capacity is based off of plastic elevator buckets of similar style. Buckets available in carbon or stainless steel. AR wear lips, back plates and venting available upon request. Buckets available in gauges including 14GA, 12GA, 10GA, 7GA, 1/4″ thick.
Tiger-Tuff Steel Digger
Bucket Size, Inches | Punching, Inches | Weight, Lbs. | Capacity, Cu. Inches | ||||||
---|---|---|---|---|---|---|---|---|---|
Size | Length (L) | Proj. (P) | Depth (D) | Centers (E) | # Of Holes | Bolt Size | 10 GA Carbon Steel | Water Level (X-X) | Useable 5° Over X-5° |
12X7 | 13-3/8 | 8-1/8 | 7 | 3-3/8 | 4 | 5/16 | 15.7 | 283.18 | 312.06 |
13X7 | 14-3/8 | 8-1/8 | 7 | 3-5/8 | 4 | 5/16 | 16.35 | 292.51 | 323.22 |
14X7 | 15-3/8 | 8-1/8 | 7 | 3 | 5 | 5/16 | 17 | 331.49 | 365.3 |
15X7 | 16-3/8 | 8-1/8 | 7 | 3-1/4 | 6 | 5/16 | 17.65 | 346.64 | 383.38 |
16X7 | 17-3/8 | 8-1/8 | 7 | 2-7/8 | 6 | 5/16 | 18.3 | 379.9 | 418.65 |
11X8 | 12-3/8 | 8-1/8 | 8-1/4 | 3 | 4 | 5/16 | 17.33 | 340.02 | 374.7 |
12X8 | 13-3/8 | 9-1/8 | 8-1/4 | 3-3/8 | 4 | 5/16 | 18.9 | 373 | 411.08 |
13X8 | 13-7/8 | 9-1/8 | 8-1/4 | 3-5/8 | 4 | 5/16 | 19.9 | 404.85 | 446.15 |
14X8 | 15-7/8 | 9-1/8 | 8-1/4 | 3 | 5 | 5/16 | 21.3 | 436.8 | 481.35 |
16X8 | 17-1/2 | 9-3/4 | 8-1/8 | 2-7/8 | 6 | 5/16 | 23.1 | 512.57 | 566.39 |
18X8 | 19-1/2 | 9-3/4 | 8-1/4 | 3-1/8 | 6 | 5/16 | 25.2 | 567.49 | 627.08 |
20X8 | 21-1/2 | 9-3/4 | 8-1/4 | 3-1/2 | 6 | 5/16 | 27 | 646.81 | 714.73 |
22X8 | 23-1/2 | 9-3/4 | 8-1/4 | 4 | 6 | 5/16 | 29.43 | 701.9 | 757.4 |
24X8 | 25-1/2 | 9-3/4 | 8-1/4 | 3-1/2 | 7 | 5/16 | 31.37 | 763.4 | 831.08 |
16X10 | 17-1/2 | 11-3/4 | 10 | 2-7/8 | 6 | 5/16 | 30 | 795.7 | 875.37 |
18X10 | 19-1/4 | 11-1/2 | 10 | 3-1/8 | 6 | 5/16 | 32.5 | 910 | 1001.21 |
20X10 | 21-1/2 | 11-1/2 | 10 | 3-1/2 | 6 | 5/16 | 35.6 | 1032.5 | 1135.98 |
Recommended Uses
(Recommended but not restricted to handling these specific products)

Barley

Brown Sugar

Coffee

Corn

Feed

Flour

Grain

Grass Seed

Meat Scap

Nuts

Oats

Pellets

Rice

Salt

Soy Beans

Sugar

Sunflower Seeds

Wheat
Poly
Application:
Grains & Food Products Temperature
Range:
-60F to +180F(210F intermittent)
FDA Approved Material:
Yes
Comments:
Economical, high density polyethylene. FDA approved material for handling food grade products.
Nylon
Application:
Hot, high impact, abrasive dense products
Range:
-60°F to +300°F (350°F intermittent)
FDA Approved Material:
No
Comments:
Best for high heat applications, with tough impact and abrasion needs.
Urethane
Application:
Heavy, abrasion, sticky materials
Range:
-60F to +180F(210F intermittent)
FDA Approved Material:
Yes
Comments:
Most flexible and abrasion resistant. Resists product sticking and sharp cutting particles.
FDA Nylon
Application:
Hot, high impact, abrasive food grade products
Range:
-60F to +300F
FDA Approved Material:
Yes
Comments:
Best for high heat food grade applications, with tough impact and abrasion needs.
Venting an elevator bucket aids in bucket fill and discharge with light, fluffy materials.
Lightweight, fluffy materials, those that are extremely dense or flow poorly can be difficult to handle in bucket elevators at high speeds. Because these materials tend to trap air when being handled by an elevator bucket, venting provides air relief to assist in their filling and discharge. Commodities for venting include flours, meals, feed mash, DDG’s or screenings. As these materials enter the bucket, air is released through a series of vent holes in the bottom of the bucket allowing for a more complete fill. These vent holes also allow air to re-enter the bucket, which facilitates full release of product into the discharge.
Standard hole diameter is equal to the size of the bolt mounting holes in vent pattern #1, all other vent patterns will have 11/32” diameter holes unless otherwise requested by the customer.
ADDITIONAL SPECIAL DRILLING AND VENTING CHARGES
- Drilling any diameter hole over 13/32″
- Bolt Hole centers closer than 1-3/4″
- Side drilled buckets except standard peanut buckets
- Special Venting requirements such as extra holes, change in hole diameter, etc.
- Quoted prices subject to change due to special drilling and venting requirements
#1 Vent
Same holes in body as bolt mounting holes.
#2 Vent
One row of holes on 1-1/8″centers
#3 Vent
Two rows of holes on 1-1/8″centers.
#4 Vent
Same as #3, plus three holes in each end cap.
Custom Vent
Vented as required.
Please call for guidance on bucket venting.
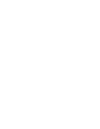
Tiger-Tuff Agricultural Buckets
What Makes Tiger-Tuff so Tough?
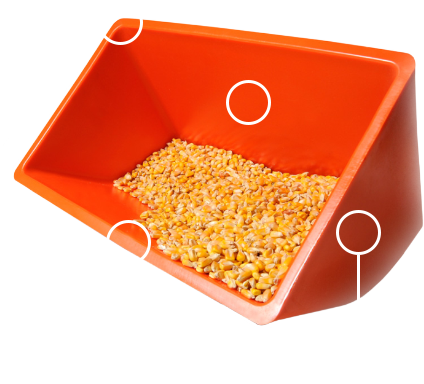
HIGH-DENSITY PLASTIC
Thicker corners handle severe abuse. Heavy front lip for superior wear. Ultra-thick walls stand up to impact.
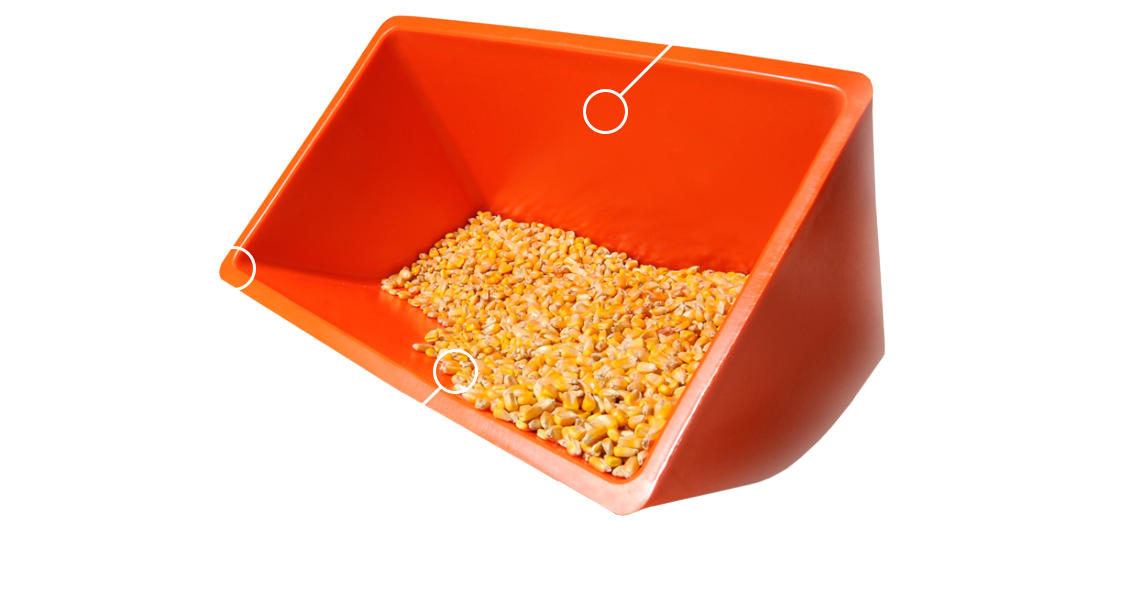
Complete your Build
A single shipment, on a single invoice, from a single source: Maxi-Lift. For a limited time only, Maxi-Lift is offering 3% OFF on new bundle orders. Contact us today or call (800) 527-0657 for more information!
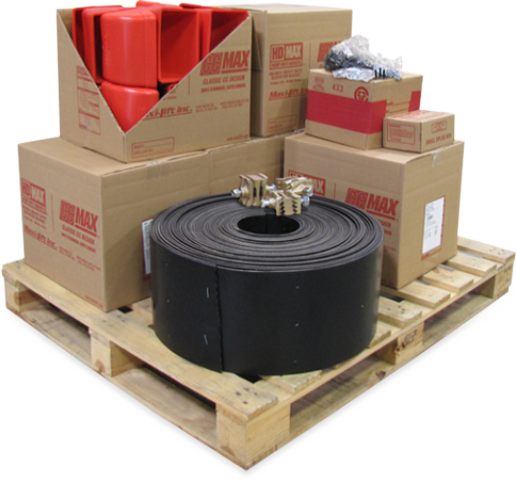
Subscribe
Join our mailing list to stay up to date with what is happening at Maxi-Lift, Inc.