
- High Grade, Lightweight Aluminum Construction
- NBR Rubber Wedge Protects Backside of Belt
- Weight: 1.93 lbs. each
- One Bolt Design
- 5/8″ x 4 1/2″ Hex Head Bolt
- Rated for belts up to 800 PIW
- U.S. Patent
- Overview
- Technical Info & Installation
- Comparison Chart
- Warning
- Media / Literature
The ULTRA features all the advantages of the SUPER splice, but with a smaller frame and a single bolt design. Designed for belts up to 800 PIW, the ULTRA also features the MAXI-SPLICE three piece construction and NBR rubber wedge for protection against belt wear. Like the SUPER, the ULTRA is designed with a larger radius for gentle belt turns.
FEATURES / BENEFITS
- High Grade, Lightweight Aluminum Construction
- NBR Rubber Wedge Protects Backside of Belt
- Template Tape Included
- Weight: 1.93 lbs. each
- 5/8″ x 4 1/2″ Hex Head Bolt
- Rated for belts up to 800 PIW
APPLICATIONS
- High Capacity Elevators
- Export Facilities
- Processing Plants
- River Terminals
- Wide Bucket Elevators
- Multiple Row Bucket Elevators
Tools Recommended
- Maxi-Lift Ultra belt punch for 11/16” Diameter holes.
- Torque Wrench capable to 150 foot pounds torque rating
- 15/16” Diameter Deep Socket
- 15/16” wrench
- Impact wrench
- Ultra Splice template tape
- C-Clamp Vise Grips to hold belt in position
- Silver pencil or Sharpie to mark belting
Installation (Download PDF Instructions)
- Follow established procedures for Lockout/Tag out of the bucket elevator.
- Ensure that belt ends are square and even. Find and mark belt center line with the silver pencil or Sharpie.
- Apply Maxi-Splice Ultra Template tape using the marked center line as a guide. See instructions on the tape backing for full details. Make sure template is squarely applied. Trim template tape excess off of belt edges.
- Use the Ultra belt punch to cut holes through the belt in the marked position.
- Pull the ends of the belt together, square up and clamp in place. Once clamped, check for square on both ends. Use the holes through the first belt as your guide to cut the holes through the second.
- Prepare the center section of each splice by installing the rubber, with any required shims per below.
a. Up to 5/16” thick belting, mount the rubber wedge, without shims, directly to the aluminum center section
b. 5/16” to 3/8” thick belting, insert one shim between the wedge and aluminum center section.
c. 3/8” to ½” thick belting, insert two shims between the wedge and aluminum center section. - Secure the wedge/shim assembly using the supplied allen key bolts and the allen wrench supplied. If reusing the screws, a fresh application of a thread lock compound is required.
- Insert the center Ultra splice wedge between the two belt ends, aligning with the drilled holes. The center wedge should be placed so the rubber wedge is toward the pulley side. Place one of the two outer plates on the belt top and align with the holes drilled in the belt. The larger radius end should be toward the pulley side of the belt. Apply one of the washers to the 5/8” grade 5 bolt and insert bolt through the holes. Bolt head should be up to protect the threads from wear during use.
- Apply the bottom plate, adding the second washer, and thread on the locking nut. Tighten until lightly snug. You will want the splices to be relatively loose at this point so they may be repositioned and squared prior to final tightening. Due to the stiffness of thicker belting, it may be necessary to use clamps to pull the belt ends together to allow the nut to be applied.
- Repeat this process until all units are in place and ready for final tightening.
- While still loosely fastened, make sure all of the Ultra splice plates are squared and properly aligned. Use the impact wrench to snug the bolts to 50 foot pounds, beginning with the outer splices, first on one side, then the other. Next, go to the center splice, tighten, and then alternate from left to right until all units are tight. Final torque should be 125 foot pounds, checked with a torque wrench.
- Once all units are fully tightened, slowly release tension on the clamps and let the belt to pull into its natural position. Replace the access panels and operate the elevator for 30 minutes running empty and recheck the torque on the splice bolts. Adjust as necessary.
- Operate the elevator under load and recheck torque again.
IMPORTANT- Due to the inherent compression properties of thicker rubber belts, it will be necessary to inspect the splice often for the first week of operation, as the belt will compress causing loss of bolt torque. Failure to do so could result in splice failure. Splice inspection should be a regular part of any maintenance program. Continue to inspect splices regularly to verify the fasteners remain in torque specification.
View/Print the Comparison Chart (PDF)
Belt Splice Technical Data Sheet
![]() | ![]() | ![]() | ![]() | ![]() | ![]() |
|
---|---|---|---|---|---|---|
PART DETAILS | Product | MAXI-SPLICE | MAXI-SPLICE | MAXI-SPLICE | MAXI-SPLICE | MAXI-SPLICE |
Brand | CI | AB | ULTRA | SUPER | TITAN | |
Part No | CI5 | AB5 | ULTRA5 | SUPER5 | TITAN | |
SPLICE CONSTRUCTION | Color | Silver | Manganese Bronze | Silver | Silver | Silver |
Construction | 3 Piece Mechanical Clamping Device | 3 Piece Mechanical Clamping Device | 3 Piece Mechanical Clamping Device with NBR (Nitrile) Rubber Wedge | 3 Piece Mechanical Clamping Device with NBR (Nitrile) Rubber Wedge | 3 Piece Mechanical Clamping Device with HNBR Rubber Wedge | |
Metal Material | Galvanized Cast Iron | Manganese Bronze | Aluminum | Aluminum | Aluminum | |
Metal Description | Ferrous Cast Iron | Non-Ferrous Bronze | High Grade, Lightweight Aluminum | High Grade, Lightweight Aluminum | High Grade, Lightweight Aluminum | |
Rubber Material | None | None | Replaceable NBR Rubber Wedge | Replaceable NBR Rubber Wedge | Replaceable HNBR Rubber Wedge | |
SPLICE SPECIFICATIONS | Weight (lbs.) | 2.6 | 2.9 | 1.93 | 4.8 | Per Application |
Length | 3″ | 3″ | 4-1/2″ | 6-1/4″ | 6″ | |
Width | 2″ | 2″ | 2-1/2″ | 3″ | Per Application | |
PIW Rated | Up to 600 PIW Tensile | Up to 800 PIW Tensile | Up to 800 PIW Tensile | 800-1200 PIW Tensile | Over 1200 PIW | |
Recommended Belt Thickness | 1/4″ to 5/8″ | 1/4″ to 5/8″ | 1/4″ to 5/8″ | 3/8″ to 3/4″ | Per Application | |
BOLT SPECIFICATIONS | No of Bolts | 1 | 1 | 1 | 2 | Per Application |
Bolt Grade | Grade 5 Hex Head Bolt | Grade 5 Hex Head Bolt | Grade 5 Hex Head Bolt | Grade 5 Hex Head Bolt | M16 10.9 Hex Head Bolt | |
Bolt Diameter (Inches) | 1/2″ | 9/16″ | 5/8″ | 3/4″ | Per Application | |
Bolt Length (Inches) | 5″ | 5″ | 4-1/2″ | 5″ and 5-1/2″ | Per Application | |
Washers | Yes | Yes | Yes | Yes | Yes | |
Nuts | Nylock | Nylock | Nylock | Nylock | Oval Lock Nut | |
Recommended Torque * | 75 ft./lbs | 100 ft./lbs. | 125 ft./lbs. | 150 ft./lbs. | Per Application | |
Template Tape Included | Yes | Yes | Yes | Yes | Requires Special Template | |
SHIMS | Required Shims Per Belt Thickness | N/A | N/A | Under 5/16” – No Shims 5/16” to 3/8” – 1 Shim 3/8” to 1/2” – 2 Shims | Under 1/2” – No Shims 1/2” to 5/8” – 1 Shim 5/8” to 3/4” – 2 Shims | N/A |
TEMPERATURE RATINGS | Max. Operating Temps | 600° F / 350° C | 500° F / 260° C | 200° F / 93° C (NBR Rubber Wedge Limiting Factor) – Alternative Wedges Available for Higher Temperatures | 200° F / 93° C (NBR Rubber Wedge Limiting Factor) – Alternative Wedges Available for Higher Temperatures | 320° F / 160° C (HNBR Hydrogenated Nitrile Butadiene Rubber Wedge Limiting Factor) |
Nylock Nut Max. Temp | 250° F | 250° F | 250° F | 250° F | 320° F | |
MINIMUM HEAD PULLEY DIAMETER | Agricultural (High Speed) ** | 12″ | 12″ | 24″ | 30″ | 48″ |
Industrial (Centrifugal/Gravity) | 12″ | 12″ | 20″ | 36″ | 48″ | |
BUCKET PROJECTION | Minimum Recommended | 4″ | 4″ | 5″ | 7″ | 8″ |
FEATURES/ BENEFITS | Strong, Standard, Mechanical Splice | Non-Sparking, Non-Corroding, Non-Rusting | Non-Sparking, Non-Corroding, Non-Rusting, Longer Belt Life | Non-Sparking, Non-Corroding, Non-Rusting, Longer Belt Life | Non-Sparking, Non-Corroding, Non-Rusting, Longer Belt Life |
WARNING: DO NOT USE ANY MAXI-SPLICE ON MANLIFTS!
Please read all instructions before installing any Maxi-Splice product. Instructions can be found at maxilift.com. Failure to follow installation instructions may result in splice failure. As with any belt splice, continuous, regular inspections are required or failure can occur.
Never mix Maxi-Splice products on a single installation. Reduced or uneven clamping pressure may occur compromising splice integrity and could result in splice failure.
Maxi-Lift neither solicits nor recommends the use of any Maxi-Splice belt clamp for splicing man-lift belts. Maxi-Splices were neither designed for nor tested for this purpose. Any installation of a Maxi-Splice product for this purpose may result in splice failure causing serious bodily harm or even death. Do not use on steel cable belts.
Do not reuse nylon insert lock nuts when reinstalling Maxi-Splices. Please use new nylock nuts for reinstallation. Replacements are available from Maxi-Lift.
For applications exceeding 250° F, nylon insert lock nuts may not be used, as this temperature range exceeds the manufacturer’s threshold for nylon integrity. Compression locking nuts should be utilized instead.
While the AB and CI Maxi-Splice may be used on wing pulleys, they may contribute to wear on the backside of the belt at the splice. It is the user’s responsibility to inspect the splice at regular maintenance intervals to prevent failure. Noise may also be heard as the splice contacts the wings of the pulley.
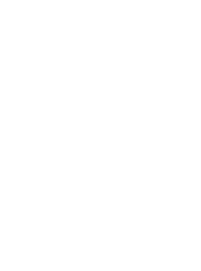
Maxi-Splice Ultra Belt Splices
Complete your Build
A single shipment, on a single invoice, from a single source: Maxi-Lift. For a limited time only, Maxi-Lift is offering 3% OFF on new bundle orders. Contact us today or call (800) 527-0657 for more information!
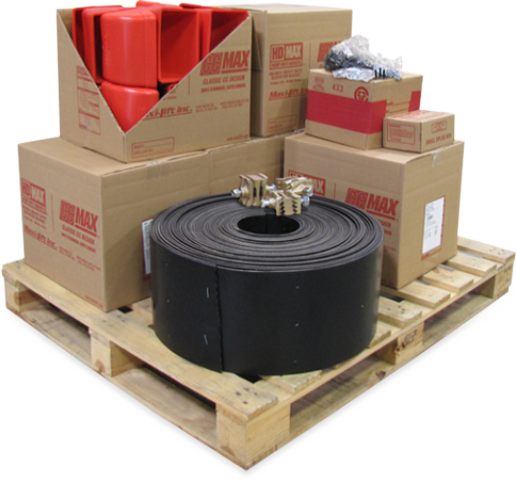
Subscribe
Join our mailing list to stay up to date with what is happening at Maxi-Lift, Inc.